Adrian_
10 W
- Joined
- Apr 12, 2022
- Messages
- 84
I have a QS 273 V3 5T motor with about 800 miles on it. Yesterday I was doing a full throttle pull from stand still when at about 20 mph the throttle cut out and the whole bike started vibrating, it felt like phase wires were shorted. I pulled over and then got a "Hall sensor" error on my display. I opened the bike up and unplugged the hall plug and inspected it, it look fine so I plugged it back in and I was still getting hall sensor error so I plugged it into the motors backup hall set as the QS motor comes with two sets of halls and the hall error went away and the bike worked fine.
After about 8 miles, the throttle cut out again and got hall sensor error. This time the main set nor the backup set was working, kept getting hall error on both so ended up walking home. What I did notice was that depending at what motor position I turned the controller on, it would either instantly give me a hall error or it would allow the bike to nudge forward a bit before cutting out throttle and giving a hall error. If I turned on the controller and didn't get the hall error, if I manually rotated the motor slightly, it would give me a hall error so to me it looked like possibly a wiring problem as I doubt two sets of hall sensors would fail after 800 miles and withing 8 miles apart from each other.
Today after the bike was sitting overnight, I turned it back on and it worked fine for about 20 feet before it cut out and gave me hall error again so I knew the problem is either inside the motor or with the wiring between the controller and the motor. I didn't bother testing the hall sensors with voltage meter, I went straight to taking the motor apart so I can continuity test all the hall wiring as a wiring problem seemed more plausaible to me than faulty hall sensors.
When I opened the motor, a decent amount of water came out and found multiple spots of corrosion on windings and even a broken winding which seems to have been caused by corrosion. After seeing that, I came to the conclusion that this was most likely the cause of my issues and the halls were fine. I took some picture.
I highlighted the corrosion and the broken winding. The other side looked in very good condidition compared to this side, only one little spot of corrision. I'm not sure if this broken winding is the cause of the hall errors. Could I even save this motor? I was thinking about letting it dry, then clean up the corrosion with a soft brush and alchohol, solder the broken winding together and use spray on insulation, seal the motor with high temp silicon and never use it in the rain again.
After about 8 miles, the throttle cut out again and got hall sensor error. This time the main set nor the backup set was working, kept getting hall error on both so ended up walking home. What I did notice was that depending at what motor position I turned the controller on, it would either instantly give me a hall error or it would allow the bike to nudge forward a bit before cutting out throttle and giving a hall error. If I turned on the controller and didn't get the hall error, if I manually rotated the motor slightly, it would give me a hall error so to me it looked like possibly a wiring problem as I doubt two sets of hall sensors would fail after 800 miles and withing 8 miles apart from each other.
Today after the bike was sitting overnight, I turned it back on and it worked fine for about 20 feet before it cut out and gave me hall error again so I knew the problem is either inside the motor or with the wiring between the controller and the motor. I didn't bother testing the hall sensors with voltage meter, I went straight to taking the motor apart so I can continuity test all the hall wiring as a wiring problem seemed more plausaible to me than faulty hall sensors.
When I opened the motor, a decent amount of water came out and found multiple spots of corrosion on windings and even a broken winding which seems to have been caused by corrosion. After seeing that, I came to the conclusion that this was most likely the cause of my issues and the halls were fine. I took some picture.
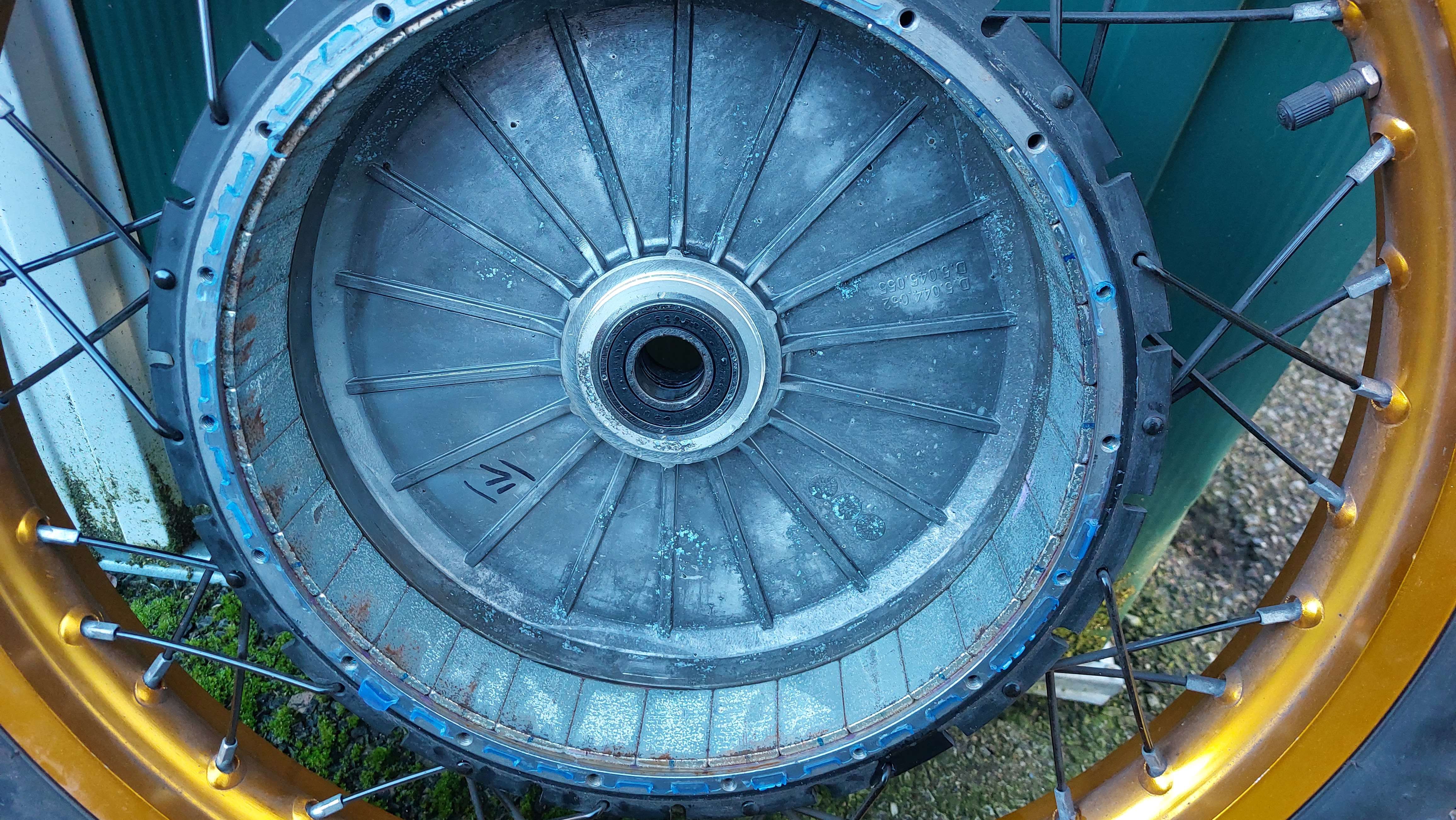
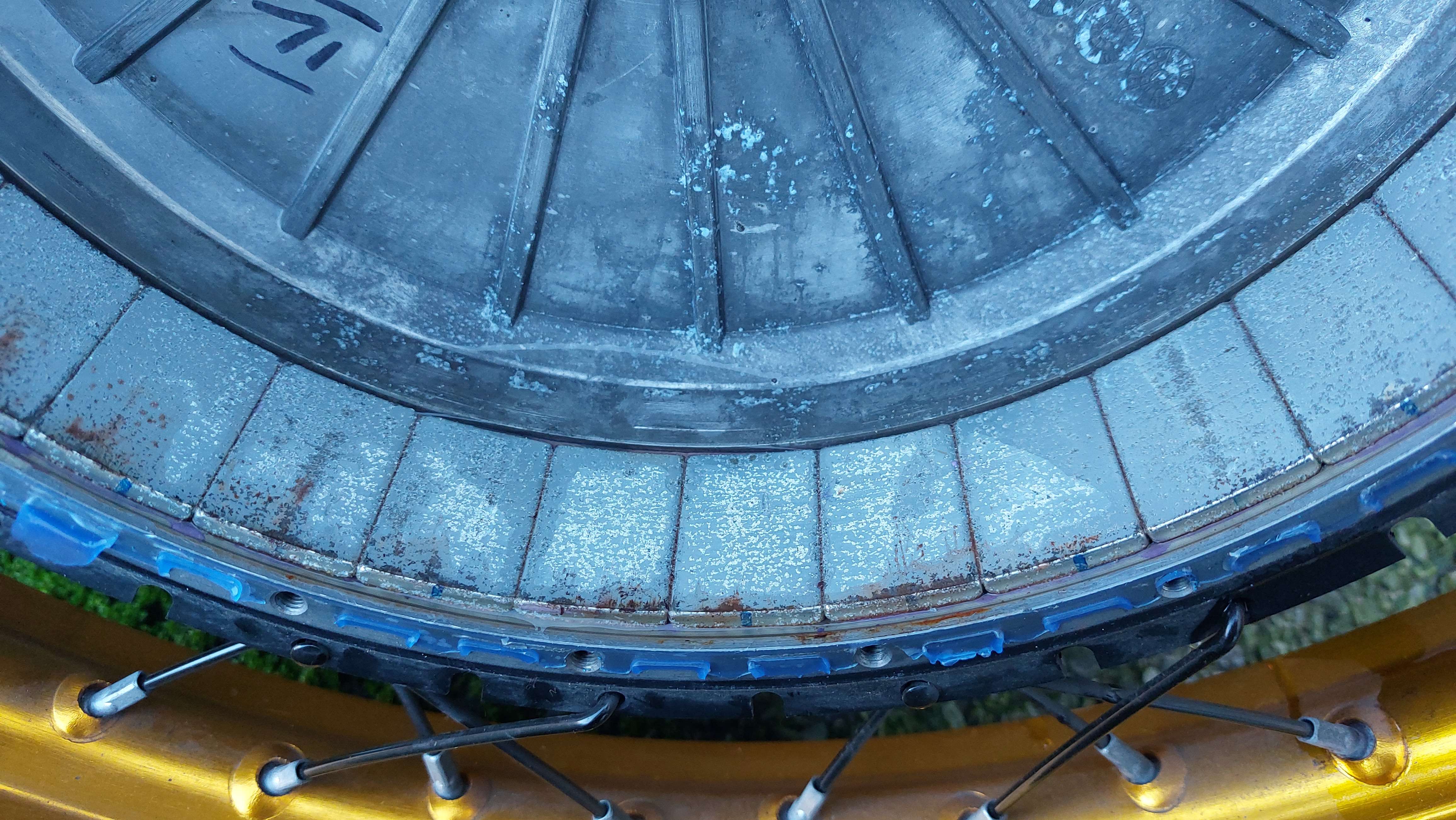
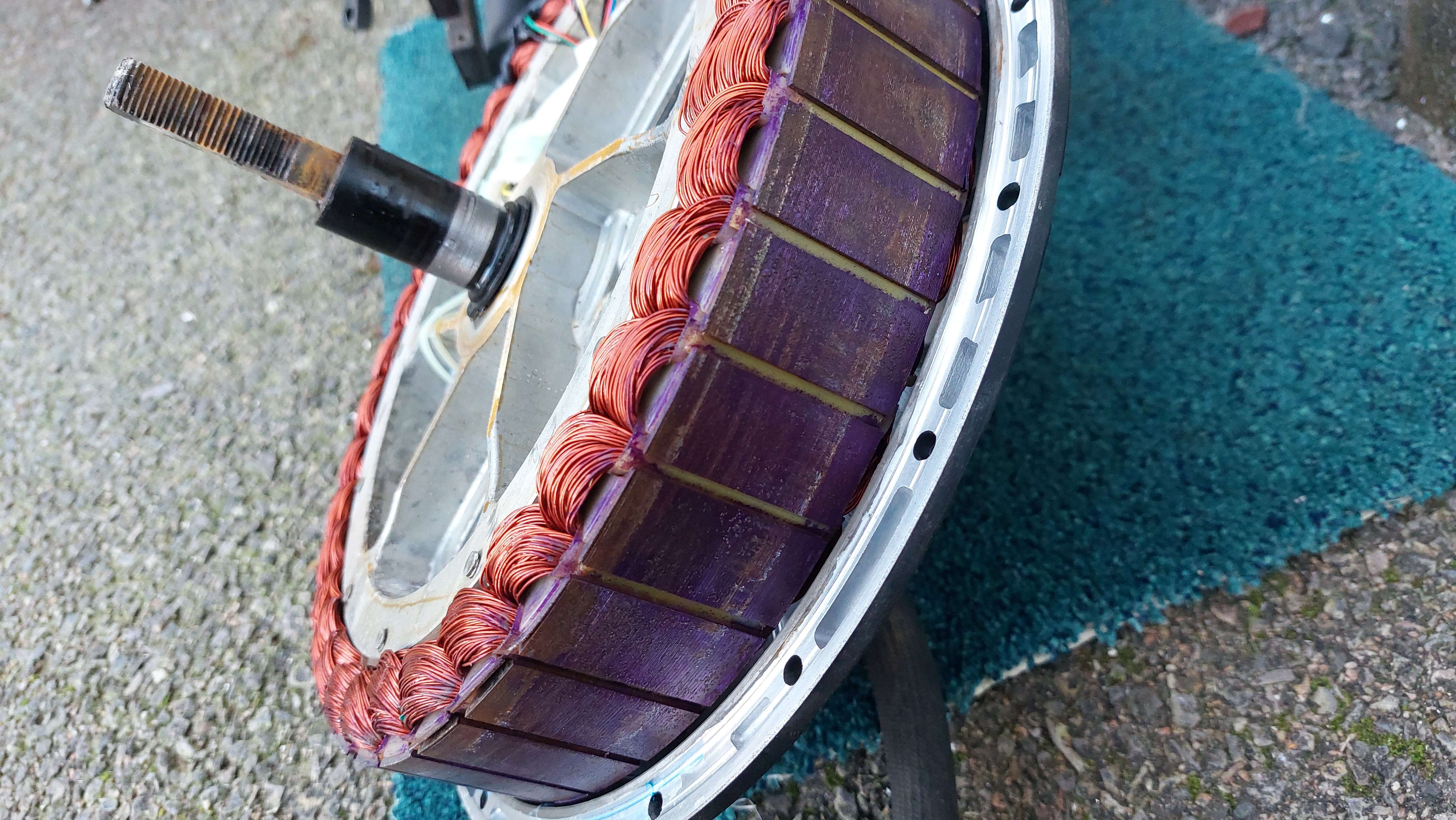
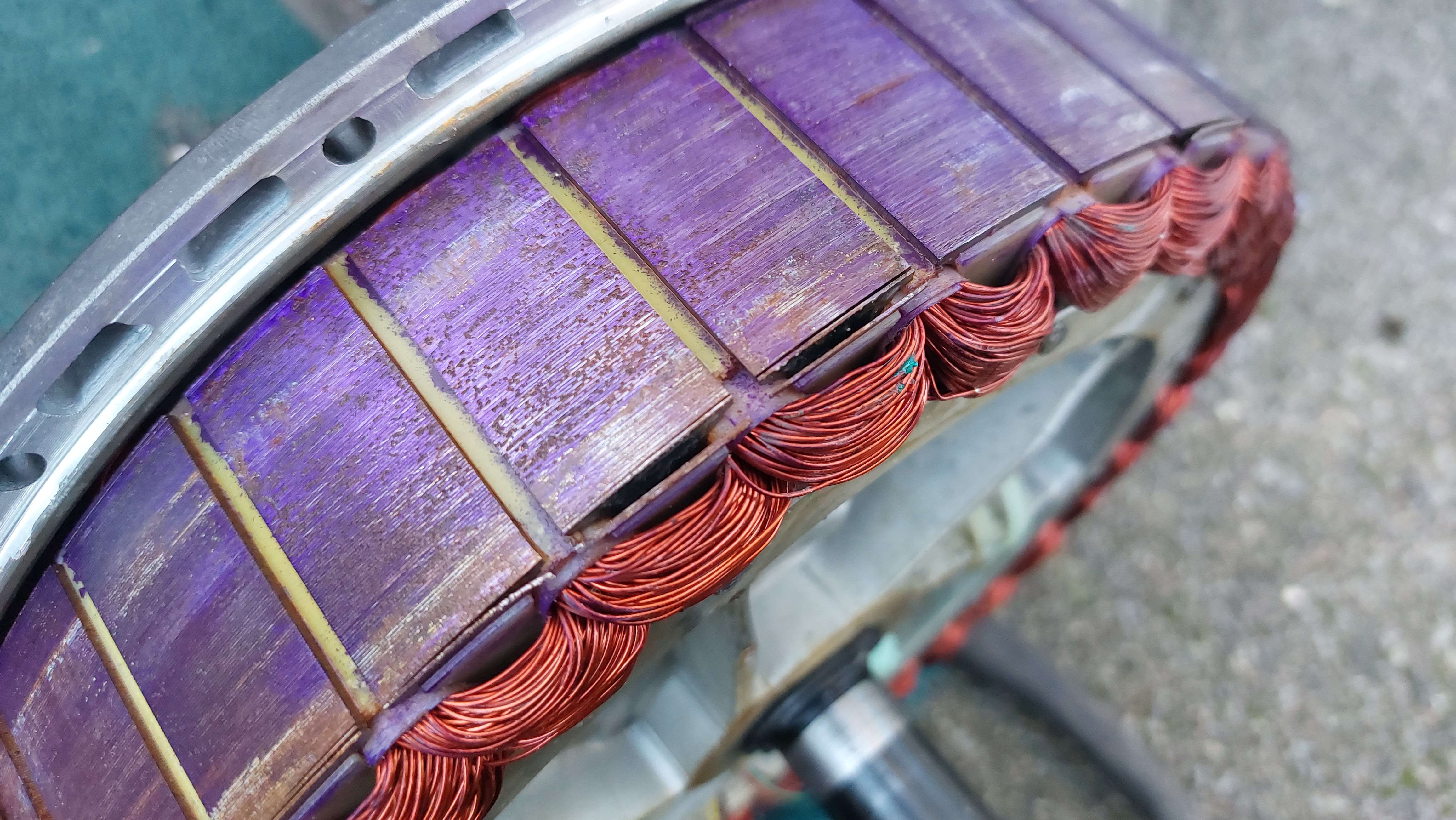
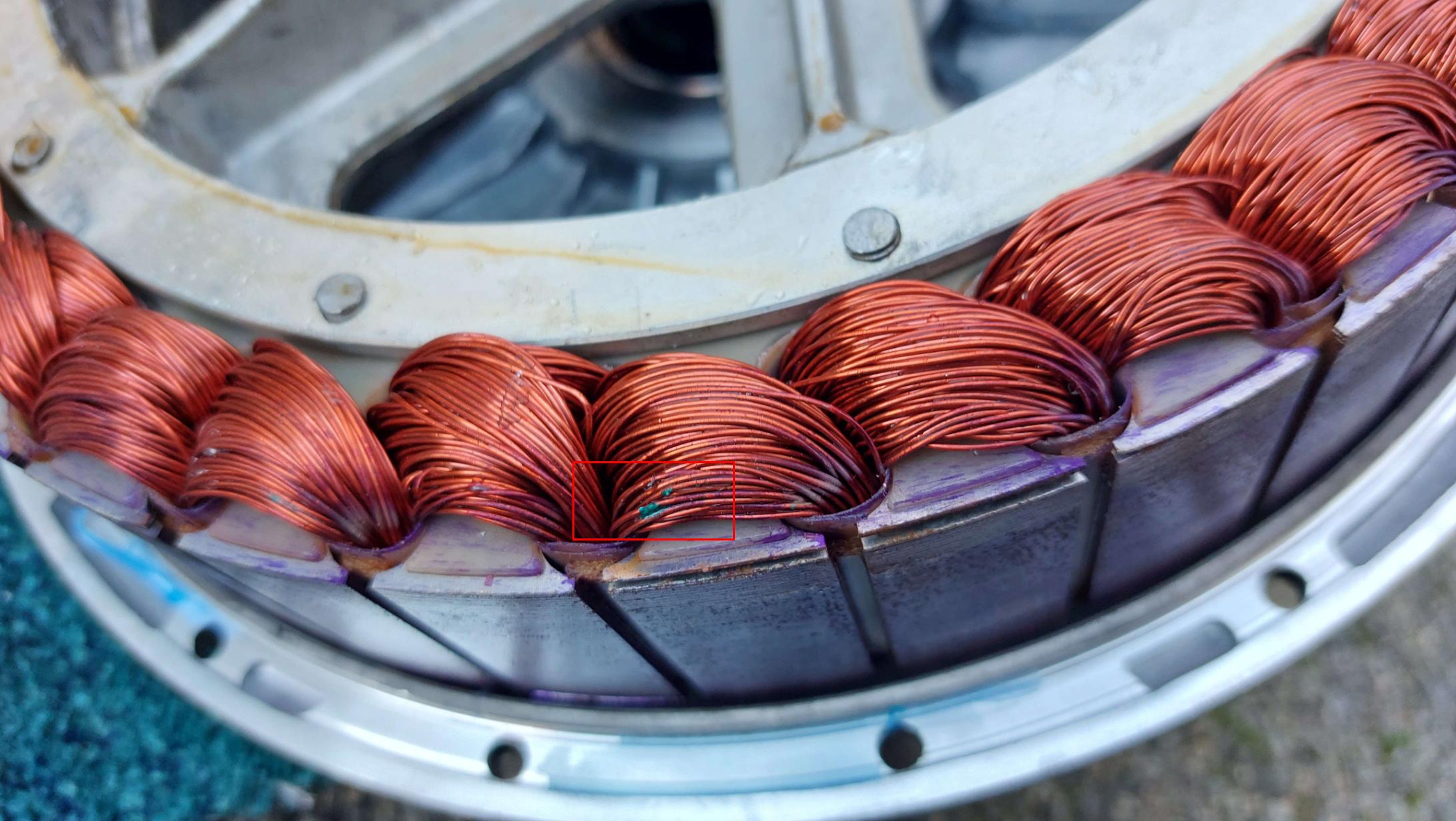
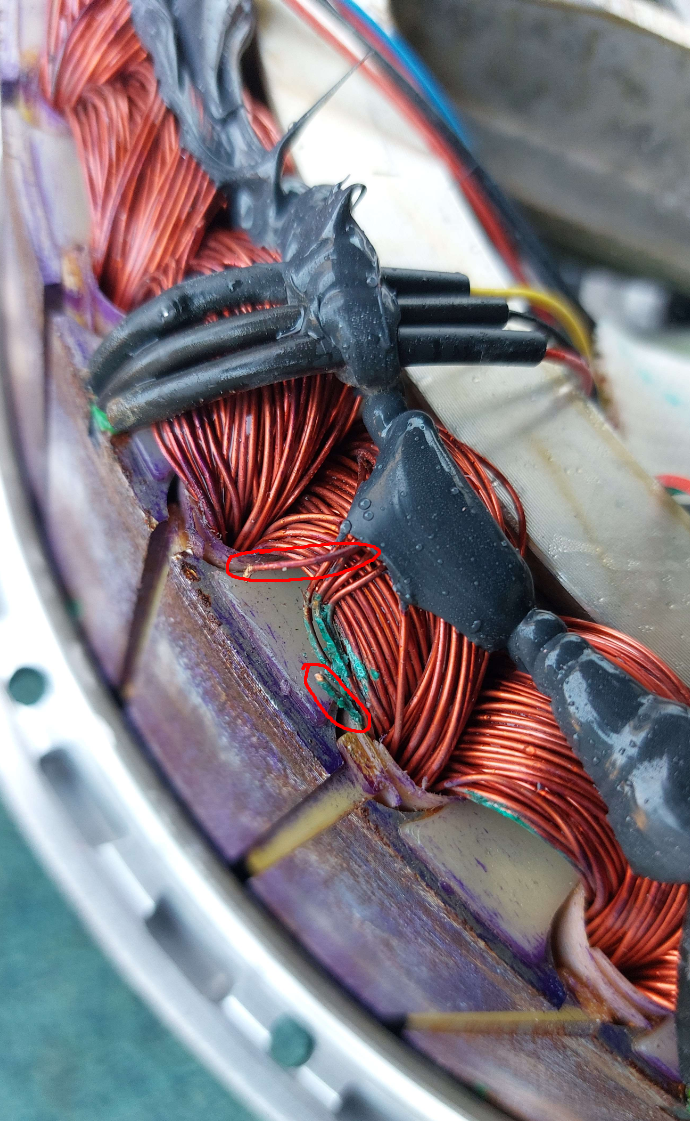
I highlighted the corrosion and the broken winding. The other side looked in very good condidition compared to this side, only one little spot of corrision. I'm not sure if this broken winding is the cause of the hall errors. Could I even save this motor? I was thinking about letting it dry, then clean up the corrosion with a soft brush and alchohol, solder the broken winding together and use spray on insulation, seal the motor with high temp silicon and never use it in the rain again.