Elektrosherpa
1 kW
- Joined
- Feb 7, 2021
- Messages
- 386
After a break due to too much work, I want to see now what the controller does (or not does) when activated again.
Can I switch it on for a first test by only connecting the thin "pwr" and "ground" cables in the plug (pink and black)
to my power source:
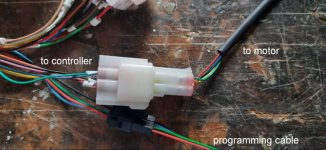
or is it absolutely necessary to connect also the fat phase wires of the motor and the main battery cables?
Can I switch it on for a first test by only connecting the thin "pwr" and "ground" cables in the plug (pink and black)
to my power source:
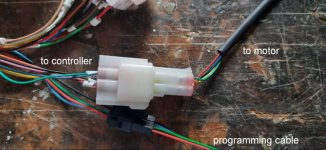
or is it absolutely necessary to connect also the fat phase wires of the motor and the main battery cables?