izeman
1 GW
just came home and started to work on it 
not installed on the bike but on my work bench to see if the android app works.
first of all i had to install phase wire connectors, and did cut off the screw terminals (still left on the battery wires in my picture below). my trusted 5.5mm gold bullets, good for up to 100A. and i must say i'm impressed. this is the first controller with adequate battery/phase wires. they just fit into the goldies perfectly fine. soldering the battery wires to my xt60 connector will be a challenge. the wire looks like a #8-10awg. well done kelly! con: they are very stiff and not fine stranded, so hard to bend. but that is only an issue during install.
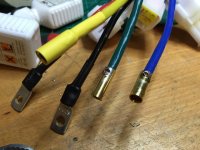
now for the bad part.
the android phone with the otg cable and my regular usb<->rs232 adapter DON'T work. just as fany from kellycontroller said. so it seems you really HAVE to buy this z-tek usb/serial converter. i already ordered one, but it will take two mode weeks to arrive. so i will have to wait with further testing.
not installed on the bike but on my work bench to see if the android app works.
first of all i had to install phase wire connectors, and did cut off the screw terminals (still left on the battery wires in my picture below). my trusted 5.5mm gold bullets, good for up to 100A. and i must say i'm impressed. this is the first controller with adequate battery/phase wires. they just fit into the goldies perfectly fine. soldering the battery wires to my xt60 connector will be a challenge. the wire looks like a #8-10awg. well done kelly! con: they are very stiff and not fine stranded, so hard to bend. but that is only an issue during install.
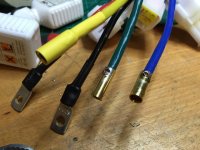
now for the bad part.