Problem: I currently have a MXUS 3K 4T motor, and I would like it to perform more like a 3T motor now that neither my battery nor my controller are limiting factors in performance. Particularly, I'd like to increase my torque above 25 MPH, exactly where the 4T under performs in comparison to the 3T winding, as well as my top speed going up hills.
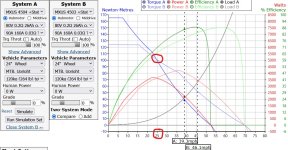
Keeping voltage and wheel diameter constant in the simulator, as I increase phase amps on the 4T, I only get more torque where I don't really care as much about it, at low RPM and over a decreasing range as phase amps goes higher. Since the motor simulator does not simulate field weakening, some questions:
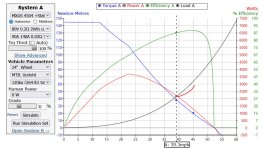
1. Is the estimated red line a somewhat accurate trendline representation of what is happening with power requirements as the field weakening current increases and motor speed/RPM approaches 45 MPH?
2. Is the simulated torque curve above 39.3 MPH still accurate using field weakening, meaning that it would be about 20 Nm at 45 MPH for the 4T winding? Or does field weakening also change wheel torque at these (over)speeds deviating from the torque trendline plotted?
3. Lastly, is the ~52 MPH shown at 0 Nm the theoretical maximum RPM achievable by this motor winding arrangement and does it also define the max limit of field weakening?
My current layman's understanding of field weakening is that while it increases RPM, it doesn't increase torque before or after the max RPM without FW so it wouldn't help me with torque over 25 MPH, nor would it help much or any in hill climbs. This leaves me with 3 options as far as I can tell if I want to stick with this ~20 lb motor design.
A) Phase wire upgrade
B) Rewinding 4T motor
C) Buy another MXUS with 3T winding.
So rewinding doesn't look fun and I'm not too keen on buying another motor, looking at option A:
Just to run the figures on a phase wire upgrade for the 4T, I'm assuming the current phase wires are ~11AWG and the length of the wires replaced is 2 feet. 11AWG resistance is 1.26 ohm / 1000 ft, so .00252 ohms for 2 feet. I could probably fit 8AWG phase wires with teflon shrink, which for 2 feet is .00126 ohms for a difference of only .00126 ohm resistance improvement over 11AWG in each phase wire. I've read that the 4T has a .110 ohm phase winding resistance. While I'm not 100% on the calculation, I'm assuming that's between 2 windings, so 2X .00126 ohm improvement is only a 2.3% resistance improvement for performing this phase wire upgrade.
Comparing the torque at 39.3MPH between the 3T and 4T winding, you have roughly 38 Nm vs 72 Nm. If lowering the phase wire resistance only 2.3% were to proportionally increase torque of the 4T motor at 39.3 MPH, that would be a ~1 Nm improvement. This seems like a total waste of time if these calculations are correct, although a 2.3% resistance improvement would be somewhat more significant at low RPM. Am I missing something?
In other words, I got one realistic option if I want to improve torque above 25 MPH without changing the battery configuration or wheel diameter, higher KV winding motor right?
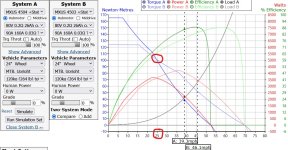
Keeping voltage and wheel diameter constant in the simulator, as I increase phase amps on the 4T, I only get more torque where I don't really care as much about it, at low RPM and over a decreasing range as phase amps goes higher. Since the motor simulator does not simulate field weakening, some questions:
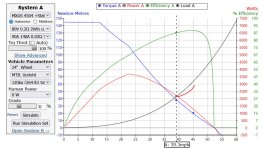
1. Is the estimated red line a somewhat accurate trendline representation of what is happening with power requirements as the field weakening current increases and motor speed/RPM approaches 45 MPH?
2. Is the simulated torque curve above 39.3 MPH still accurate using field weakening, meaning that it would be about 20 Nm at 45 MPH for the 4T winding? Or does field weakening also change wheel torque at these (over)speeds deviating from the torque trendline plotted?
3. Lastly, is the ~52 MPH shown at 0 Nm the theoretical maximum RPM achievable by this motor winding arrangement and does it also define the max limit of field weakening?
My current layman's understanding of field weakening is that while it increases RPM, it doesn't increase torque before or after the max RPM without FW so it wouldn't help me with torque over 25 MPH, nor would it help much or any in hill climbs. This leaves me with 3 options as far as I can tell if I want to stick with this ~20 lb motor design.
A) Phase wire upgrade
B) Rewinding 4T motor
C) Buy another MXUS with 3T winding.
So rewinding doesn't look fun and I'm not too keen on buying another motor, looking at option A:
Just to run the figures on a phase wire upgrade for the 4T, I'm assuming the current phase wires are ~11AWG and the length of the wires replaced is 2 feet. 11AWG resistance is 1.26 ohm / 1000 ft, so .00252 ohms for 2 feet. I could probably fit 8AWG phase wires with teflon shrink, which for 2 feet is .00126 ohms for a difference of only .00126 ohm resistance improvement over 11AWG in each phase wire. I've read that the 4T has a .110 ohm phase winding resistance. While I'm not 100% on the calculation, I'm assuming that's between 2 windings, so 2X .00126 ohm improvement is only a 2.3% resistance improvement for performing this phase wire upgrade.
Comparing the torque at 39.3MPH between the 3T and 4T winding, you have roughly 38 Nm vs 72 Nm. If lowering the phase wire resistance only 2.3% were to proportionally increase torque of the 4T motor at 39.3 MPH, that would be a ~1 Nm improvement. This seems like a total waste of time if these calculations are correct, although a 2.3% resistance improvement would be somewhat more significant at low RPM. Am I missing something?
In other words, I got one realistic option if I want to improve torque above 25 MPH without changing the battery configuration or wheel diameter, higher KV winding motor right?